Equipment Tracking Form For Construction Using Form Builder
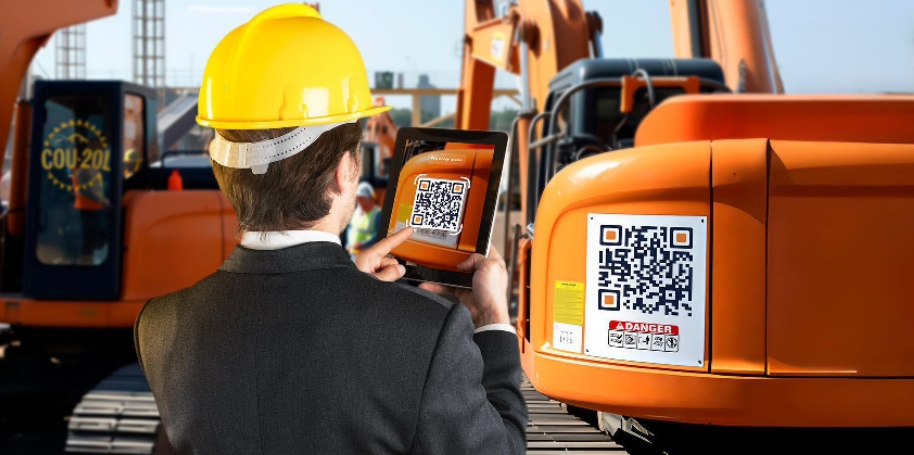
The global construction equipment market reached about $195 billion in 2023 and is expected to grow to around $274 billion by 2031. This underscores the need for accurate and effective tracking to reduce breakdown.
A digital equipment tracking form for construction companies provides a more straightforward way to manage assets. It also reduces losses and keeps safety standards on track. Well-organized equipment management is crucial on construction sites, where even minor delays can lead to high costs.
If you want to know how construction teams can use an online form builder to organize assets and maintain workflows, here’s your ultimate guide.
Digitizing your tracking forms offers streamlined inventory tracking. As a result, you can pay less tax and avoid fines while booking and checking assets. It also helps you manage maintenance successfully.
Apart from that, here are more reasons why equipment tracking forms for construction are important:
Enhance project management performance
Proper equipment tracking allows construction managers to connect equipment status with project management.
By accessing real-time data, teams can successfully enhance workflows and divide resources to avoid delays. This alignment improves the construction project management process and confirms that projects stay on schedule and within budget.
Compliance with equipment safety standards
Tracking construction equipment is vital for both safety and compliance. Companies can guarantee regular inspections and necessary workplace maintenance by simply keeping accurate records, reducing risk of accidents.
In 2022, the U.S. construction industry reported 1,092 fatalities, one of the highest of any sector. Complying with construction equipment safety standards reduces the risk of accidents and legal issues.
Reduces losses due to misplacement or theft
Theft often occurs at construction sites, resulting in equipment losses that range from $300 million to $1 billion annually in the U.S. By implementing an equipment tracking form, companies can reduce losses from theft or misplacement. This strategy enhances accountability and optimizes the use of valuable resources.
Enhance maintenance scheduling
Regular updates on conditions are crucial for keeping a construction equipment maintenance schedule and preventing failures. They provide valuable insights into usage patterns, helping teams avoid expensive repairs.
Benefits of a free form builder for construction equipment tracking
Tracking and maintaining construction equipment can be complex and time-consuming. A free form online builder offers an efficient, user-friendly solution for real-time management.
Here’s how this reliable tool can enhance equipment oversight and keep records accurate:
Real-time asset updates
When construction employees spot hardware malfunctions in equipment, it’s important to know how, why, where, and why it happened. An easy-access tracker comes in handy.
Each piece of equipment features a QR code that construction workers can scan. This allows them to access real-time information about its location, status, and usage history.
By scanning the code, workers can easily verify a machine’s status, whether it is out for repair or awaiting maintenance. This process minimizes delays and reduces confusion.
Simplified maintenance management
Scheduled maintenance is crucial for keeping equipment operational. With a free equipment tracking form for the construction industry, workers can access the maintenance history and status with a single scan. Here is how the form simplifies maintenance management:
- Tracking Maintenance Needs: Online tracking forms can provide equipment maintenance schedules and will notify teams when services are due.
- Organized Record Keeping: Each scan can track new information about usage, damage, or repairs, creating a complete digital history for every piece of equipment.
Reduced paperwork and improved productivity
Digitizing equipment tracking forms reduces paperwork and streamlines data collection and storage. Workers can input data into digital forms by scanning QR codes instead of entering information on paper. These QR code-based forms minimize human error and ensure accurate information is accessible to site managers and safety inspectors.
How to set up your equipment tracking form online
You can implement QR code-enabled tracking forms in a few straightforward steps. Here’s how to set up a form for tracking equipment:
Step1: Choose the right form builder
When choosing a digital form software, focus on ease of use and alignment with your industry’s needs. Consider the tool requirements and the service costs—free or subscription-based. Also, check if you can print codes using standard printers.
In addition, look for customization options in the form builder, such as colors, logos, sizes, and shapes. Ensure the generator allows syncing QR codes with updated asset details.
Step 2: Design the equipment tracking form
An equipment tracking form for construction should be concise. It must include essential fields for managing equipment. Consider adding fields for:
- Equipment Identification Number
- Location
- Usage Hours
- Last Maintenance Date
- Conditions
The form should be easy for workers to complete and designed for mobile use to ensure smooth data entry.
Step 3: Generate and attach QR codes to each equipment
Once your form is ready, generate a unique QR code using an online form builder that links directly to the tracking form for each piece of equipment. Attach these QR codes to the equipment in a visible, accessible place for easy scanning.
Step 4: Train your team on QR code usage
Introduce your team to the form QR code tracking system. Give clear instructions on scanning QR codes, filling out the form, and updating equipment status in real-time. Encourage workers to use company mobiles or personal smartphones to access QR code tracking forms easily.
Streamline efficiency with QR-enabled tracking for construction equipment
QR-coded equipment tracking forms for construction companies streamline maintenance, reduce downtime, and improve equipment safety.
A quick scan gives easy access to equipment data, helping teams ensure each machine meets safety and maintenance standards. This approach reduces losses and ensures compliance with industry safety protocols. Deploy a digitized tracking system for your construction company using a trusted software today.